Stone Processing Laboratory
2
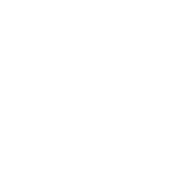
Stone Processing Laboratory
Patents
The fastest sampling time
Products Category
The process begins with the creation of high-quality abrasive filaments. These filaments are produced using advanced extrusion techniques to ensure consistency and durability.
The plastic bases for the abrasive brushes are created using injection molding. This ensures a precise fit and strong foundation for the filaments.
The manufactured abrasive filaments are then cut to the required lengths and carefully assembled onto the plastic bases, ensuring even distribution and secure attachment.
The assembled filaments are glued onto the plastic bases and allowed to dry. This step ensures that the filaments remain firmly in place during use.
Each abrasive brush undergoes a thorough quality inspection to ensure that it meets SleekEven’s high standards for performance and durability. Only products that pass this rigorous inspection are approved for shipment.
High-quality raw materials are carefully selected and blended to create the optimal mixture for the grinding discs. This step ensures the consistency and performance of the final product.
The blended raw materials are precisely measured and loaded into molds. This process is crucial for achieving the correct shape and size of the grinding discs.
The molds filled with raw materials are then heated in a pressing machine. This step applies the necessary pressure and temperature to bond the materials together, forming a solid and durable grinding disc.
After the heating and pressing process, the newly formed grinding discs are carefully removed from the molds. This step requires precision to maintain the integrity and shape of each disc.
The grinding discs are then subjected to a gluing process to ensure that any additional components or layers are securely attached. This step enhances the strength and functionality of the discs.
Each grinding disc undergoes a thorough quality inspection to ensure it meets SleekEven’s high standards. This includes checking for any defects, verifying dimensions, and testing performance. Only discs that pass this rigorous inspection are approved for shipment.
Selection and preparation of high-quality alloy and diamond powders to ensure the durability and performance of the saw blades.
Mixing diamond powders with alloy powder, followed by pressing and sintering to create robust diamond segments that provide the cutting edge.
Cutting and shaping the steel substrate to the desired dimensions, ensuring it meets the specific design requirements for the saw blade.
Attaching the diamond segments to the steel substrate through a hot press sintering process, which fuses them together under high temperature and pressure.
Ensuring the saw blade is perfectly straight and balanced to prevent wobbling and ensure precise cuts during use.
Conducting thorough inspections and tests to verify that the saw blades meet strict quality standards, ensuring reliability and performance.
High-quality raw materials are meticulously selected and prepared. This step ensures that the base materials are clean, pure, and mixed to the precise specifications required for producing top-grade abrasive filaments.
The prepared raw materials are fed into an extrusion machine, where they are heated and forced through a die to form continuous abrasive filaments. This process is crucial for achieving uniform thickness, consistency, and optimal abrasive properties.
Once extruded, the filaments are cooled and wound onto spools or cut into manageable lengths for easy handling and transportation. This step ensures that the filaments are stored in a way that maintains their quality and prevents damage.
The filaments are then cut to the required lengths based on customer specifications or the intended application. Precision cutting ensures that each filament meets the exact standards needed for efficient performance in abrasive tools.
Every batch of filaments undergoes a rigorous quality inspection process. This includes checking for consistency in diameter, tensile strength, and abrasive properties. Only filaments that pass this stringent inspection are approved for use in SleekEven's abrasive products.
Our factory is equipped with the latest CNC machines, allowing for precise and efficient production of complex stone processing tools. This technology enables us to meet the exact specifications and high-quality standards required by our customers.
SleekEven's quality control system includes multiple inspection stages, such as raw material testing, in-process checks, and final product verification. Each product undergoes rigorous testing to ensure it meets international quality standards before it leaves our factory.
Our dedicated research and development team continually innovates to improve product performance and introduce new solutions. Recent advancements include the development of longer-lasting abrasive brushes and more efficient cutting tools, setting new benchmarks in the industry.
We are committed to sustainability, utilizing eco-friendly materials and energy-efficient processes. Our factory has implemented waste reduction programs and recycles materials wherever possible, reducing our environmental footprint and promoting a greener future.
SleekEven can customize stone cutting and grinding tools for granite, marble,sandstone, artificial quartz etc.
Contact us now to get a free sample.
Free SampleWe have stone tool experts who will provide you with the best grinding and cutting solutions quickly and for free.
Contact Now